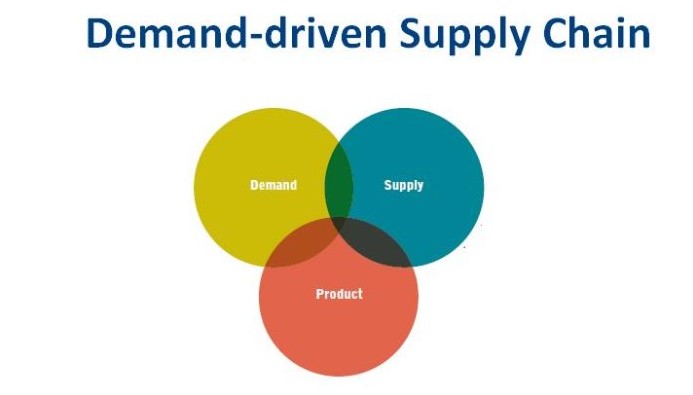
Demand driven MRP is an innovative approach to supply chain management that aims at improving the efficiency of a company’s supply chain by anticipating and managing fluctuations in demand for various goods and services. This method of management seeks to improve companies’ profitability by improving their overall profit margin. The key advantage of demand-driven MRP is that it takes into account the real-life requirements of a company and addresses these needs on the appropriate time. This in turn reduces the cost, risks and time involved in supply chain management and allows a company to respond quickly to changes in demand.
Demand driven supply chain planning, therefore, is a methodology that identifies the most profitable time to introduce new goods into an already established supply flow. The primary objective of demand-driven supply chain planning is the development of a demand-driven supply chain, shaped by collaboration between the production, processing and retail phases of the supply cycle. This planning approach should be grounded in the ability to forecast demand in terms of both quantity and quality. This enables a company to plan for any changes in demand that may occur and to adjust its operational procedures and systems accordingly.
Many companies choose to use demand-driven supply chain planning in order to gain an upper hand in price competition in their markets. This strategy not only helps to provide a competitive edge over rivals but also helps to ensure maximum use of existing product capabilities. Large scale demand planning facilitates the seamless transition of existing assets into the most appropriate production process and offers a number of significant advantages. Some of these advantages include the following.
* Cost savings – Using efficient planning methods can dramatically reduce the costs involved in production. When a company is able to effectively monitor its activity, it is in a position to suggest and implement measures which will achieve its business objective. By ensuring that any unnecessary activity is eliminated before it begins, companies can free up resources for more productive production activities. By coordinating production across multiple sites and locations, this leads to increased efficiency and reduces costs further still. In addition, such processes lead to improved coordination with partner companies and a reduction in overall factory overheads.
* Improved performance – It is possible to design a production process which is more effective, more efficient and less costly. Once such a system has been developed, it can be used as the basis for developing additional processes. These additional processes are developed to meet the requirements of the particular product or market placed before the original plan was developed.
* Improved flexibility – It is possible to fine-tune demand driven processes once they have been developed. As demand varies both domestically and internationally, it is possible to take the time to fine tune the production process until it is operating at maximum capacity. In doing so, it is then possible to ensure that the company’s resources are fully available to meet any demand placed upon them. In so doing, it ensures that the company does not experience any form of manufacturing constraint. This leads to increased profitability and increased levels of employee motivation to succeed.
* Improved reliability – The planning process provides a reliable guide to identify and address any problems associated with the manufacturing processes. This occurs through a systematic review of the process and the identification of risks to the implementation of the plan. Through such risk assessments, any potential issues can be identified and managed. This leads to an increase in the reliability of the process and its execution. It is also possible to refine the process based on feedback received from other departments and external agencies.
* Improved control – The planning process gives management the tools, information and the control necessary to successfully control all aspects of the supply chain. This includes inventory levels, material flow, customer service, delivery, pick and pack and more. When such control is properly implemented, the entire process will become more efficient, thereby increasing the company’s profitability and reducing operating costs. This also leads to improved customer satisfaction since customers will receive products that have been prepared based on process specifications and delivered according to schedule.